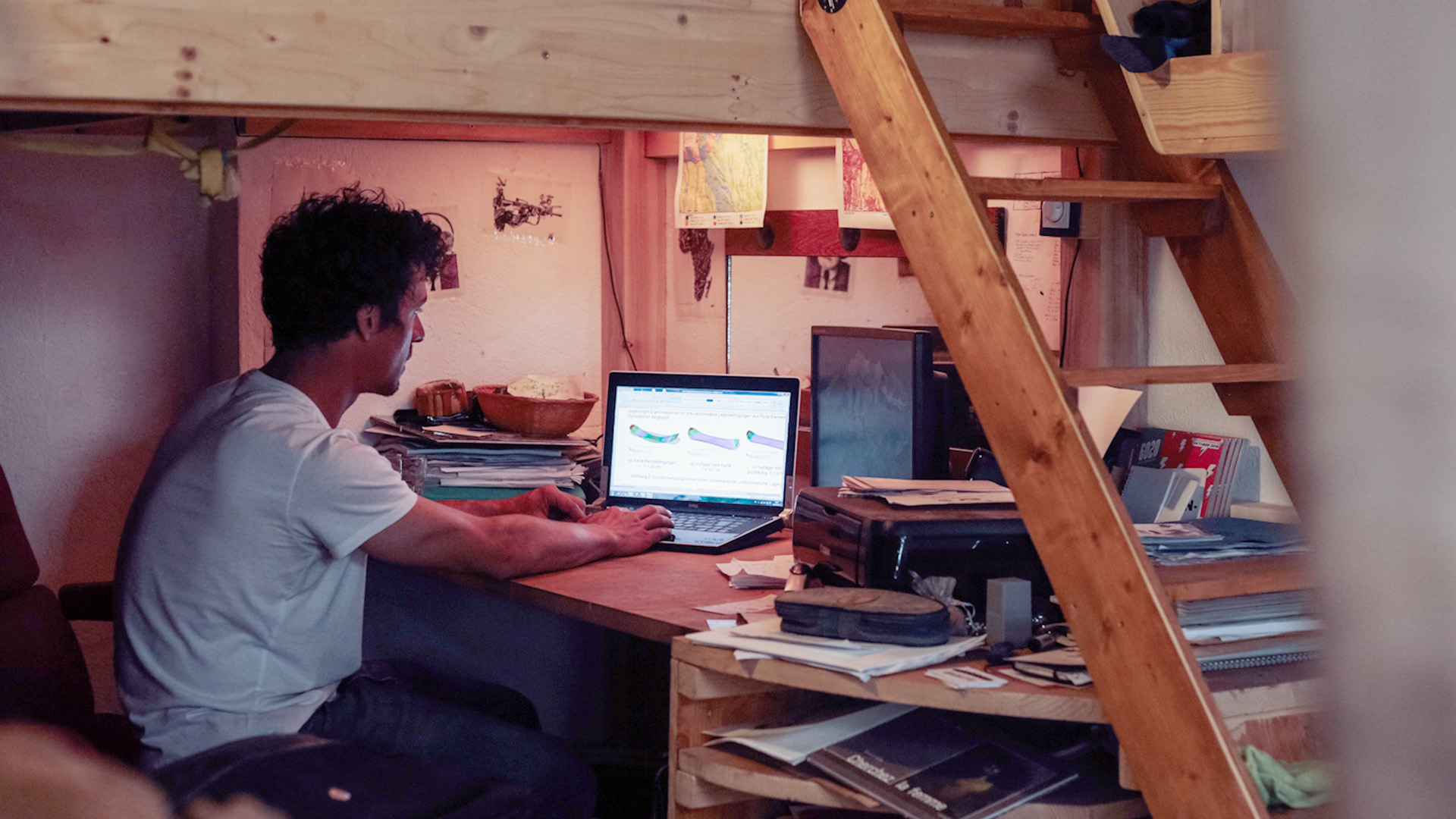
Technology
STRUCTURAL ANALYSIS
Engineering sciences provide tools for studying the behaviour of a snowboard submitted to a particular loading environment. The models implemented provide a deeper understanding of the riding mechanics and help to steer product development, improving design, weight and performance. George Box, a famous mathematician once wisely said: “All models are wrong. But some are useful…”
NUMERICAL SIMULATIONS
A digital replicate of a snowboard interacting with the rider and the mountain can be foreseen to predict the behaviour of the structure within its environment. The deformations, material stresses or edge pressure can be evaluated by means of structural analysis, where various numerical shapes can be virtually created and optimized for a specific rider profile. To ensure that the computer predictions match with the reality, full-scale experiments are set up in our laboratory. A static load bench simulating the conditions of a carved turn was developed, where the boards are tested in idealized conditions. The deformations and the interface contact pressure are measured experimentally and compared to the simulations, showing maximum differences of less than 5%. The model validation was the object of a peer-reviewed scientific publication in 2019 in the Sports Engineering Journal.
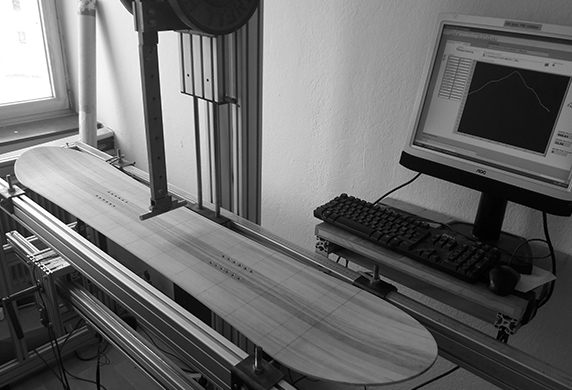
A PHD IN SNOWBOARD
ENGINEERING
In 2022, Ben completed his doctoral studies at the University of Innsbruck, on the topic “Numerical Optimization of Winter Sports Equipment”. Ground-breaking discoveries were made, opening up a whole new world of technological innovations.
Opening the Pandora’s Box. Enabling the use of natural materials by optimizing the structural load path. Improving the carving performance by controlling the edge grip during a turn. Guarantee the safety of use by tuning the eigenfrequencies, to reduce structural vibrations. Increase the stoke level by optimizing the pop of your board, or the float of your nose in powder! With the numerical tools developed in this thesis, it is now possible to make your board ride virtually before we actually manufacture it. So that even if we never built that exact shape before, we already know how it rides! Part of this research was gratefully financed by the Region Tirol, with the attribution of the grant TWF-Tiroler Science Fund for the project ZAP850003, “Optimal Sidecut Geometry of flexible Structures under Contact”.
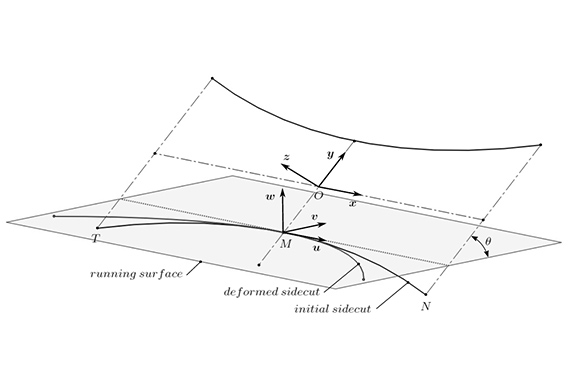
CURVATURE STORIES
The problem of the carved turn can be stripped down to the basic kinematics of a concave sidecut line being pressed against a flat, rigid surface. The deformations required to achieve tied contact can be expressed with mathematical functions, depending on the angle on which the board is tilt. In particular, the bending curvature is found to relate to the curvature distribution along the initial sidecut line. Furthermore, the Euler-Bernoulli beam theory tells us that the contact pressure occurring under the snowboard edge relates to the fourth derivatives of the sidecut function, which can be understood as the rate of change of the curvature along the initial sidecut line. This analytical model revealed the occurrence of local reaction forces at the sidecut extremities, which could be avoided with more advanced geometries. These ground breaking results were published in 2021 in the renowned scientific journal Acta Mechanica.
REPRESENTING THE SNOW PROPERTIES
The mechanical properties of snow are complex and versatile. Due to a highly porous nature and a strong sensitivity to temperature variations, it behaves very differently from most solids or granular materials. Different types of snow conditions can nevertheless be represented via the numerical representations, by considering a contact interaction model representing the snow hardness and simulating the penetration of the edge through the snow surface. While carving on harder snow, the pressure load experienced along the sidecut line is strongly dictated by the geometry of the sidecut line, interface with the mountain. The deformations are complied by the structural stiffness of the snowboard, which dictates how bending and twist deformations combine under contact conditions. The results of this study were presented at the International Snow Science Workshop conference in Innsbruck, 2018.
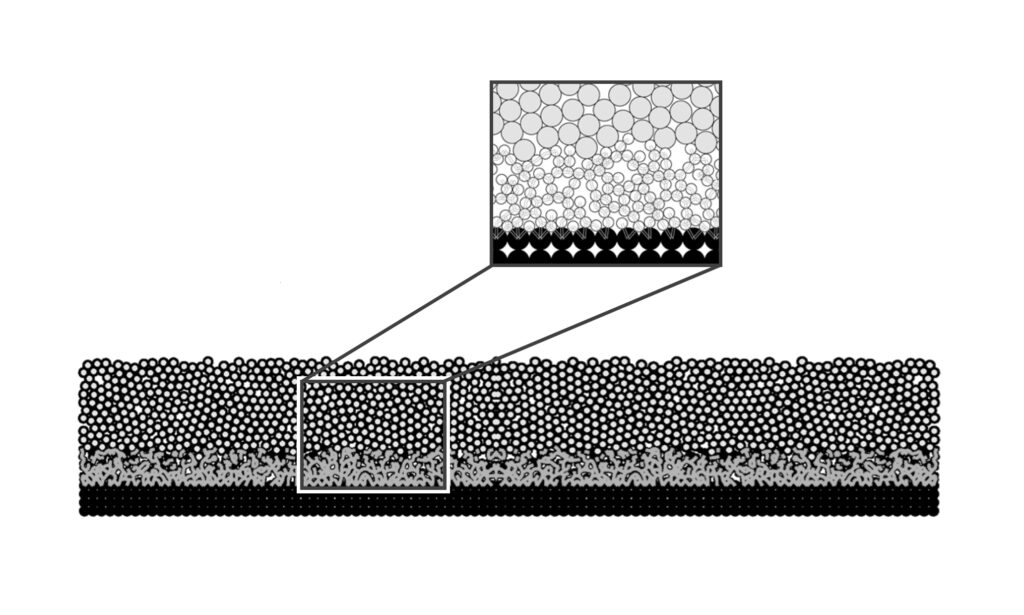
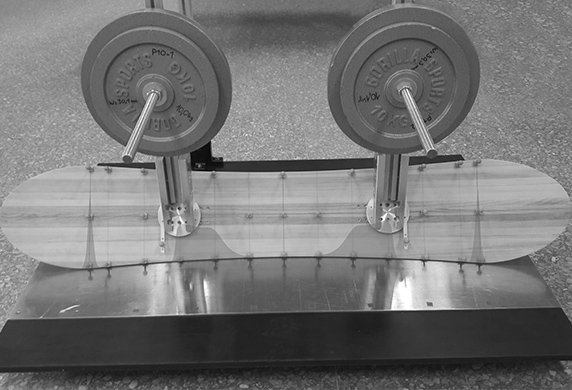
IMPROVING YOUR EDGE GRIP
The contact pressure distribution between your sidecut line and the mountain determines the personality of your board while carving. It makes it more aggressive or easier to drift, gives you edge grip or release where needed. This contact pressure happens to be incredibly sensitive to the initial geometry of your snowboard. When the sidecut geometry describes the simple arc of a circle, the pressure distribution happens to be very discontinuous and exhibits high pressure peaks. In this study, we searched for a more advanced geometry that would lead to the lowest pressure load, distributed uniformly along the sidecut line. We could achieve 82% reduction of the contact pressure by tweaking the edge line locally by not more than 1.4mm! This difference is barely perceptible to the naked eye, and yet resulting in such a large change in the riding behaviour. There lies a little bit of the beauty of snowboarding, within this often contra-intuitive problem showing a high sensitivity to small initial variations.
HOW HIGH CAN YOUR OLLIE REALLY BE?
The Ollie is one the most basic trick in snowboarding, and refers to jumping the board all the way off the ground. It is widely used in freestyle snowboarding where other tricks are built upon, as well as in freeride conditions for playful control in deeper snow or in backcountry freeriding. The Tail of the board is used to generate an upward momentum : through a backwards lean and a dynamic impulsion on the back leg, the rider lifts off the ground by using the springback properties of the structure. A board is said to have a good “pop” when the tail is snappy enough to kick back and makes you jump higher. But really, how high can an Ollie be?